Parar o processo quando uma falha é encontrada (e resolvê-la): esse é o fundamento do Jidoka. O método é um dos pilares do Sistema Toyota de Produção e em inglês ficou conhecido como “autonomation” – analogia com “automação”, mas incorporando a autonomia do operador, o aspecto humano. Por esse fundamento, os equipamentos devem ser automatizados para identificar condições anormais e interromper o trabalho. Dessa forma, o operador pode reconhecer a causa-raiz do defeito e impedir que ele se reproduza.
A excelência operacional e a qualidade de produtos e serviços são atributos indispensáveis à competitividade. Assim, identificar e evitar defeitos e falhas é um dos principais alvos do Lean Six Sigma. É por isso que o Jidoka se torna tão útil e importante na produção. Ao analisarmos a forma como executamos cada processo, o método pode ser aplicado em diferentes situações. Não apenas em máquinas por meio de autonomation, como também em sistemas logísticos e de serviços, por exemplo. Trata-se de garantir a qualidade ao longo do processo em vez de inspecioná-lo apenas no final.
O princípio pode ser dividido em alguns passos simples:
- Descobrir uma anormalidade
- Parar o processo
- Corrigir o problema imediatamente
- Investigar e corrigir a causa-raiz
A base do Jidoka parte da criação de mecanismos de identificação das falhas. De fato, a origem do método data de 1896, quando Sakichi Toyoda (fundador do Grupo Toyota) criou um dispositivo simples que automatizou a detecção de falhas em um tear. Dessa maneira, um operador poderia gerenciar vários teares e não cuidar de apenas uma máquina. Sakichi Toyoda é um dos mais destacados inventores japoneses, reconhecido como líder da Revolução Industrial no país.
Por que implantar o Jidoka?
A verificação da qualidade dos processos apenas pela observação humana pode ser um desafio. Sem dúvida, detectar todos os defeitos e manter a plena atenção ao longo dos turnos de trabalho é quase impossível. Os ciclos de cada máquina variam, e os operadores podem não conseguir reagir com rapidez suficiente a fim de evitar danos. Por outro lado, a tarefa tende a tornar-se entediante, o que também provoca a redução da atenção.
No controle de qualidade, a tendência natural é realizar uma inspeção dos produtos no final do processo. No entanto, isso gera mais custos e desperdício, uma vez que os materiais finalizados precisam ser descartados ou corrigidos. Assim, lotes inteiros podem ser rejeitados por um defeito que deveria ser identificado na raiz.
Mesmo quando pensamos em serviços, a avaliação de qualidade costuma ser feita apenas após sua realização. Isto é, as pesquisas de satisfação com os clientes trazem resultados daquilo que já ocorreu – e que muitas vezes não pode ser revertido. Nesse sentido, apostar em mecanismos de detecção de problemas traz mais chance de ter um cliente satisfeito.
Vantagens de usar o Jidoka
- Rapidez na detecção de problemas já nas fases iniciais
- Redução de custos de materiais ao evitar a produção com falhas
- Redução de custos com pessoas, pela automação de processos
- Menor desgaste de equipamentos com a parada automática em casos de anormalidade
- Mais autonomia no chão de fábrica, já que os operadores devem ser orientados para resolver os problemas encontrados
- Como uma das bases do Lean, ajuda a disseminar a cultura de melhoria contínua, mudando padrões de comportamento
- Tem menor custo que a automação total de processos, além de atender a situações em que a automação total não pode ser aplicada
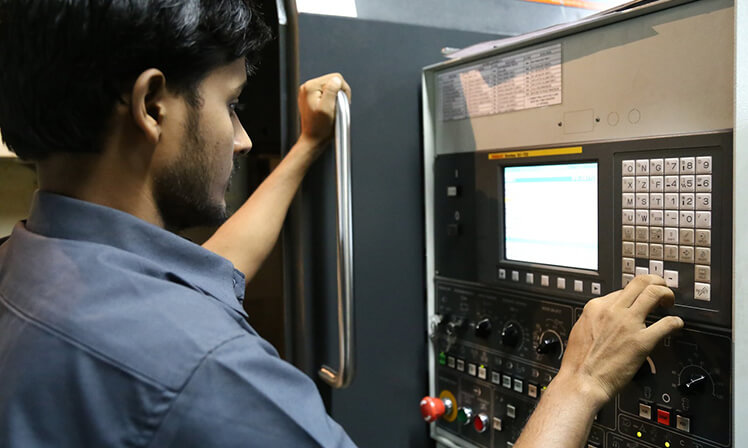
Dificuldades no caminho
Somos pressionados diariamente para produzir mais e com maior velocidade. Muitas vezes, essa pressão acaba por desestimular o controle de falhas, pois parar a produção significa “perda de tempo”. De fato, trabalhar com o Jidoka pressupõe parar a produção sempre que necessário para identificar e corrigir as anormalidades encontradas. Entretanto, esse não é um tempo “perdido”. Pelo contrário: aperfeiçoar o processo é o que garante chegar a um fluxo contínuo.
Acima de tudo, empresas que adotam a filosofia Lean não podem apresentar resistência à identificação de problemas. Isso enfraquece e até mesmo inviabiliza o uso adequado da metodologia. As interrupções nos processos podem ser muitas – e às vezes dolorosas para as equipes. Em contrapartida, sem elas não é possível avançar nos aspectos de qualidade, produtividade e excelência operacional. As paradas são a única forma de resolver de forma eficiente as dificuldades encontradas no processo. Além disso, quando essas avaliações e correções são realizadas com eficácia, rapidamente o número de paradas começa a diminuir.
Nesse sentido, é importante destacar outro desafio encontrado nas empresas: muitos dos problemas detectados são ignorados. Vemos isso com frequência, falhas antigas, que são conhecidas pela gestão, mas não são combatidas. É o velho clichê de “aqui sempre foi assim”. Ao mesmo tempo, há negócios que consideram que o erro “faz parte”. Só se esquecem de mensurar quanto de dinheiro perdem com isso…
As máquinas hoje produzidas já incorporam a autonomation, com sensores e sistemas de correção. Ainda assim, depende de nós tomar medidas para corrigir o problema e resolver a causa-raiz. Por isso, operadores e supervisores precisam ter responsabilidade e autonomia para interromper a produção quando necessário, e também para encontrar soluções. As melhorias devem ser registradas, com o propósito de comunicar as falhas e avanços e disseminar o aprendizado.
Para saber mais sobre excelência operacional e sua aplicação em pequenas, médias e grandes empresas, fale com a gente! E siga nossos posts no Facebook.
Edição: Svendla Chaves – jornalista
Imagens: Martinelle e Pashminu Mansukhani/Pixabay
Profissional de Excelência Operacional e Business Intelligence!
Sou um eterno aprendiz ou seja um pseudo-Engenheiro e Administrador de Empresas, embora nunca tenha sido um exemplo de “excelência” em Matemática, ao longo dos anos passo a maior parte do meu tempo tentando aprender a mesma e, particularmente, a estatística uma vez que, salvo muito engano, é ela que rege nossas vidas na busca da Excelência seja como pessoa ou como profissional.